4000-5000KG/H Animal Feed Pellet Production Line in Trinidad and Tobago
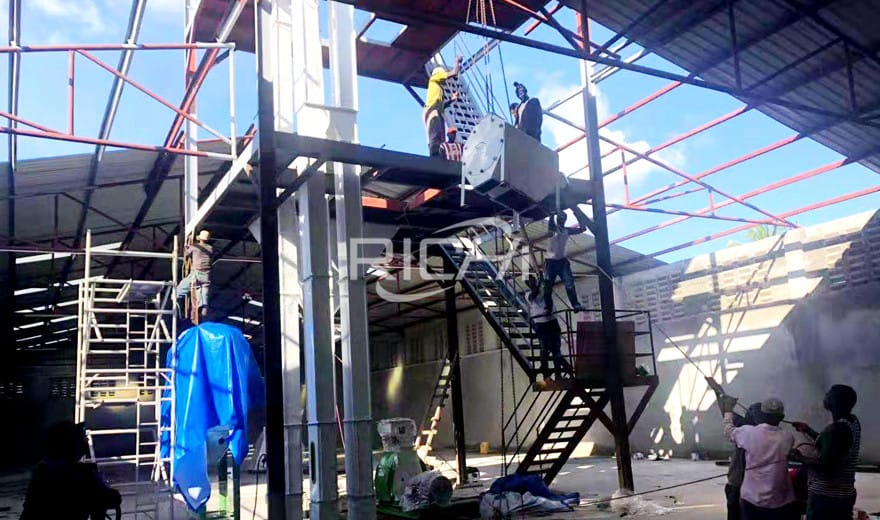
-
Country:Trinidad and Tobago
-
Application: Animal Feed Pellet Production Line
-
Output:4000-5000KG/H
The 4000-5000KG/H feed pellet production line is not the first export of Richi Machinery to Trinia and Tobago. Prior to this, we also exported the country's wood pellet processing equipment to customers in this country. In addition to petroleum and chemical products, livestock are the main products exported by Tobago, which means that there is a large demand for animal feed. The production of 4000-5000kg per hour capacity for Trinia and Tobago, where the breeding industry is not developed, it is already a relatively large production.
The general process flow of the 4000-5000KG/H feed pellet production line: put soybean, soybean meal, bran, corn and other raw materials into the cleaning equipment, the raw materials after debris removal have entered the pulverizer, and after grinding into powder, enter the mixer, according to customer's formula, oils are added in this section, and then mixed with the powdered raw materials, and then enter the feed granulator machine. The conveyer is used to put the feed pellets into the cooling machine. The cooled pellets enter the classification screen,finally enter the packaging system and prepare for storage.
The whole animal feed processing line of this project has a reasonable process layout and the production line is smooth and simple; the project is equipped with a series of high-yield and low-consumption products such as Richi's grain hammer mill, single-shaft animal feed mixer, hot sale small animal pellet food pellet machine, feed pellet cooler, screen machine, and packaging scale. In terms of the operation intensity of the workers and the same output, the equipment configured by Richi can reduce the energy consumption of at least 200kw per hour than the peer manufacturers, which reduces the operating cost of the production line. This animal feed pellet production line is a turnkey project of Richi Machinery, which has created a good model effect for similar production lines.
Feedback from customers:
Richi has good equipment performance, high degree of system automation, relatively intelligent control system, and excellent quality of overall equipment and external equipment. This project is a turnkey project, which shortens the construction period, reduces transaction costs, eliminates conflicts between the implementation links, and even reduces our construction risks. We are very satisfied!